Comprehending the Essentials of Plastic Shot Molding Processes
Plastic injection molding serves as a cornerstone of modern production, offering a systematic strategy to producing intricate elements with accuracy. Exploring these essential elements could expose just how even minor adjustments can lead to considerable renovations in manufacturing results, elevating concerns about the capacity for advancement in this well-known procedure.
What Is Plastic Injection Molding?
Plastic injection molding is a widely used manufacturing process that transforms polycarbonate and thermosetting products right into precise and complicated shapes. This strategy is preferred for its capacity to create high volumes of similar get rid of extraordinary accuracy, making it a vital method in different markets, including auto, durable goods, and medical tools.
The procedure involves thawing the selected plastic product and injecting it into a mold and mildew under high pressure. The mold, made to the specifications of the preferred component, enables the molten plastic to take shape as it strengthens and cools down. As soon as the product has actually solidified, the mold is opened up, and the finished part is expelled.
Plastic shot molding offers several advantages, including lowered waste, uniformity in manufacturing, and the capability to incorporate complex styles that might be testing with various other manufacturing methods. Additionally, it supports a broad variety of materials, each supplying special residential or commercial properties that can be tailored for details applications. As sectors proceed to introduce, plastic shot molding stays at the leading edge, allowing the advancement of sophisticated products that meet developing customer needs.
The Injection Molding Process
The shot molding procedure is an innovative strategy that includes a number of essential stages to produce top quality plastic components. Initially, plastic pellets are fed right into a warmed barrel where they are thawed into a viscous fluid. This molten plastic is then infused under high stress into a precision-engineered mold, which forms the product right into the desired kind.
When the mold is filled, the plastic is permitted to strengthen and cool, taking the shape of the mold and mildew tooth cavity. Cooling time is crucial, as it influences the cycle time and the last homes of the molded component. After sufficient air conditioning, the mold and mildew opens, and the ended up element is expelled utilizing ejector pins.

Products Used in Shot Molding
Numerous products can be utilized in the injection molding process, each offering distinct residential properties that accommodate particular applications. The most typically utilized materials consist of thermoplastics, thermosetting plastics, and elastomers.
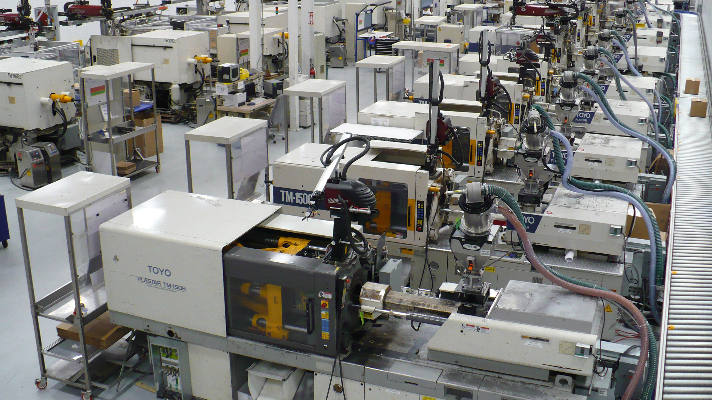
Thermosetting plastics, like epoxy and phenolic resins, go through a chemical change during the healing procedure, causing a stiff, inflexible structure. These materials are perfect for applications calling for high heat resistance and architectural integrity, usually utilized in automotive parts and electric insulators.
Elastomers, consisting of silicone and rubber-based materials, give versatility and resilience. Their distinct properties make them appropriate for applications that require flexibility, such as gaskets and seals.
Additionally, specialty materials like bio-based plastics and compounds are acquiring traction for their environmental benefits and improved efficiency features, widening the scope of injection molding applications in various industries. Understanding the residential properties of these products is critical for picking the appropriate type for specific jobs.
Advantages of Injection Molding
Injection molding stands out as a highly reliable production procedure that uses many advantages for producing complex parts with accuracy. Among one of the most considerable benefits is the ability to develop detailed layouts that would be challenging or impossible to accomplish with other approaches (Plastic Injection Molding). The procedure enables comprehensive features and limited tolerances, guaranteeing premium elements
Additionally, shot molding is understood for its rapid manufacturing capacities, making it an ideal selection for high-volume production. As soon as the mold and mildew is produced, components can be produced quickly, click here now lowering lead times and raising general productivity. This performance not only lowers manufacturing costs yet likewise gives an affordable side in the marketplace.
The adaptability of materials utilized in shot molding even more boosts its charm. A large range of thermoplastics and thermosetting polymers can be used, allowing makers to select materials that ideal meet their details requirements, consisting of versatility, toughness, and heat resistance.
Furthermore, the process decreases waste, as excess product can commonly be reused and recycled. This sustainability aspect contributes to a minimized ecological influence, making injection molding a responsible manufacturing option. Generally, the advantages of shot molding make it a preferred method for many markets.
Variables Affecting Product Quality
While various variables can browse around this web-site influence product quality in injection molding, comprehending these aspects is critical for achieving optimal results. Key elements include material selection, processing parameters, and mold design.
Material selection plays a vital role, as various polymers show one-of-a-kind buildings that influence flowability, toughness, and thermal security. Insufficient material option can result in problems such as warping or insufficient dental filling.
Handling specifications, including temperature, stress, and cycle time, need to be thoroughly controlled. Variations in these setups can lead to disparities in part measurements and surface coating. For circumstances, excessively high temperatures might trigger degradation of the polymer, while poor stress can result in brief shots.
Mold design is just as crucial, as it identifies the circulation of the molten plastic and the cooling procedure. Badly designed mold and mildews may cause unequal air conditioning rates, causing recurring tensions and dimensional errors.
Conclusion
In conclusion, plastic shot molding functions as an essential production procedure that makes it possible for the reliable manufacturing of top notch elements. Mastery of the injection molding procedure, consisting of the understanding of products and the influence of various variables on item top quality, is essential for attaining optimum results. The advantages of this approach, such as cost-effectiveness and layout versatility, further highlight its significance across numerous markets, solidifying its status as a preferred selection for high-volume production.
Plastic injection molding offers as official source a foundation of modern production, supplying a methodical strategy to creating complex parts with precision.Plastic injection molding uses several benefits, including reduced waste, uniformity in production, and the capacity to integrate intricate styles that may be testing with other producing methods (Plastic Injection Molding). As markets continue to introduce, plastic shot molding stays at the forefront, allowing the growth of sophisticated items that meet advancing consumer needs
The shot molding process is an innovative technique that includes numerous vital stages to generate premium plastic parts.In conclusion, plastic shot molding offers as a vital production process that allows the reliable production of premium components.